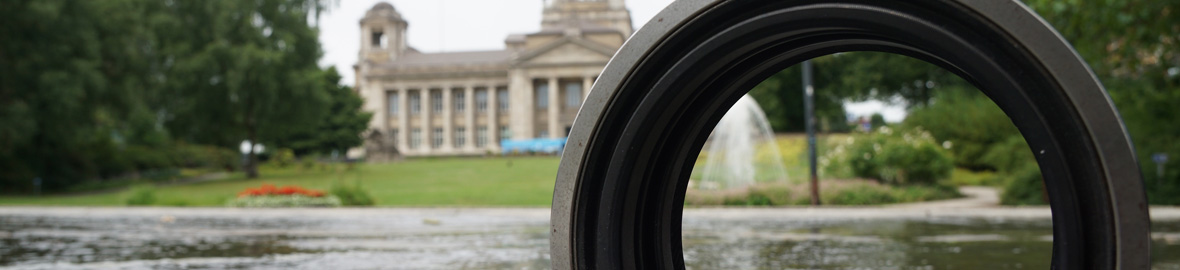
Radial oil seals
There is a lot to be said about radial oil seals. Much is technical, much scientific and much quite complex. If we were to present all of this here, we would end up with a breadth and depth extending far beyond what is really essential.
The essential is and remains: the best products and the maximum processing reliability for your own individual applications.
Accordingly, at this point we will be concentrating on the essential. We will be bringing you fully up to date with developments and presenting you with brief details of our radial oil seals in concentrated form.
However, it goes without saying that if you require any further details or should have any related questions, please do contact us and we will be happy to support you.
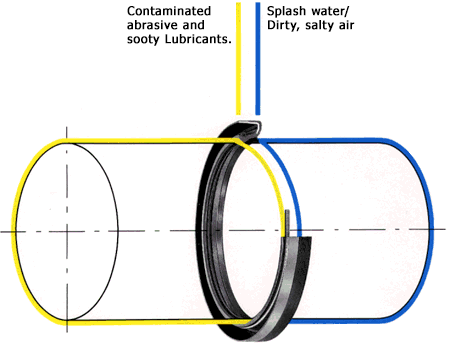
Radial oil seal FAQs
What are radial oil seals?
Radial oil seals are used to seal machine housings to prevent them being impaired in their function due to contained elements escaping. These include rotating machine elements (internal impairment) and dirt contamination (external impairment).
The choice of proper seal depends on the predominant operating parameters. Apart from the operating medium, operating temperature, rotational speed of the shaft and the pressure involved, these parameters also include the environmental conditions on the atmospheric side.
The radial oil seal consists of an elastomer component, a reinforcing ring and a spring. Specifically:
- The external surface guarantees reliable static sealing. It secures the radial oil seal in place in the casing.
- The external cover consists either of an elastomer or metal material.
- The reinforcing ring provides the radial oil seal with the required stability. The sealing lip is also pre-tensioned by a spring. This guarantees that the sealing lip makes secure radial contact right around the shaft. A protective lip is also available as an option, preventing the penetration of dirt and dust from the outside.
The other special advantage of the radial oil seal is that with its simple construction it is easy to install or remove.
What is the purpose of the oil seal?
The function of radial oil seals is to guarantee functional tightness, and therefore guarantee the reliability of the process as a whole. The aim is to keep secondary mechanical influences on the shaft to a minimum, so as to reduce the generation of heat and loss of performance within the sealed environment to the lowest possible level.
Where do we find oil seals in use?
Radial oil seals are used to seal rotating machine elements such as axles, hubs and shafts. They are used in a large number of sectors, including:
- transmission technology
- the agricultural and construction machinery industry
- domestic and industrial washing machines
- the wind power industry
- shipbuilding
- the pump industry
- rolling mills.
What standards are applicable?
Radial oil seals comply with the DIN 3760 standard.
What construction types are there?
We differentiate between three basic types:
- Construction type A features an elastomer external cover guaranteeing outstanding static sealing properties.
- Construction type B is characterised by a metallic external surface which guarantees that the seal is seated firmly and precisely within the casing.
- Construction type C – used in conjunction with construction type B – provides the degree of enhanced rigidity necessary for more demanding installation conditions and the more severe operating conditions, through the use of a reinforcing ring.
What external surface finishes are available?
For the most part, our radial oil seals are available with an elastomer external cover or an AW external surface. We also produce combinations of these in the form of special designs for special requirements.
Rubber-enclosed external surface, construction types A and AS
Radial oil seals of construction type A often feature a smooth external cover in an elastomer material. This guarantees static tightness in the casing bore,
even in critical situations. Also available with an AS protective lip.
Properties and applications:
- Excellent static sealing.
- Can be used with split casings, with any edge break or offset ends.
- With light metal casings susceptible to a high degree of heat expansion (casings with a greater expansion coefficient than steel).
- With thin-flowing or gaseous media.
- For pressurised applications within the limiting operating parameters.
- Sealing for greater degrees of surface roughness.
- Avoids the creation of frictional corrosion.
- Avoids damage to the casing bore during assembly and dismantling.
Grooved, rubber-enclosed external surface: construction type AW
To reduce compression force and to improve static tightness, the elastomer external cover is peripherally grooved.
Properties and applications:
- Easier to install due to lesser compression force.
- Reliable static sealing, especially for casings generating greater amounts of heat.
- Avoids the radial oil seal being left in an offset position.
Metallic external surface, construction types B and BS
With radial oil seals of construction type B, the smooth metallic external surface of the reinforcing ring has been finely ground, drawn or turned,
as opposed to covered. Also available with BS protective lip.
Properties and applications:
- Firm and precise seating in the bore.
- More cost-effective, due to reduced proportion of elastomer.
- External surface provided with a narrower press fit tolerance.
- Good surface quality required for casing bore.
- Not suitable for use in split casings (also with seal-lock coating, only suitable for use in split casings to a limited extent).
- Where the casing generates a lot of heat, rough bore surfaces, pressurised applications or thin-flowing creeping media, an additional sealing compound should be applied to the external surface.
In order to prevent corrosion, after final processing the metallic external surface is coated with anti-corrosion oil or has a thin coating of wax applied to it.
Metallic external surface with reinforcing ring, construction types C and CS
Radial oil seals of construction type C feature the same smooth and metallic external surface as those of construction type B. They can be provided with
the metallic reinforcing ring and are also available with a CS protective lip.
Properties and applications:
- In more demanding installation conditions, heavy-duty operating conditions and for larger dimensions.
- Radial oil seals of construction type C offer greater rigidity than radial oil seals of construction type B.
- Construction type C is extremely sensitive to installation faults.
Partially rubber-enclosed external surface: construction type A/B
Special version of external surface of radial oil seal (not held in stock). This combines the advantages of construction types A and B. Construction type A/B can also be used with casings subject to greater degrees of heat expansion and split casings. Construction types A/BS and AW/BS are also possible.
What additional sealant materials are used?
For enhanced static sealing in the casing bore, radial oil seals with a metallic external surface are frequently coated with sealing lacquer or sealing compound. Waxes or sealing lacquers are applied to protect against corrosion.
The sealing lacquer smoothes out processing traces on the external surface of the radial oil seal as well as any unevenness in the casing bore, as well as dealing with greater degrees of heat expansion. It also protects against damage to the casing bore during installation or dismantling.
Sealing lacquers are available in a variety of colours.
What material is used for springs?
The material normally used for standard springs is unalloyed spring steel to DIN EN 10270-1.
What materials are used for the reinforcing ring casing?
The standard material used is unalloyed steel to DIN EN 10139. Stainless and acid-resistant steel is used as a special material.
What materials are used for radial oil seals?
Depending on construction type and area of application, there is a variety of standard and special materials available for radial oil seals.
Elastomer materials are designated in accordance with the relevant DIN ISO 1629 and ASTM D 1418 abbreviations. Chemically produced synthetic rubber is used as the basic material for elastomer materials for radial oil seals. The individual elastomers are differentiated by their basic polymer.
The finished material is produced by mixing the basic elastomer with the corresponding auxiliary processing materials, vulcanisation materials, fillers, accelerators, softening agents and other additives.
With this as the basic procedure, it is possible to adjust the desired material properties to allow for the production of both standard materials and special mixtures.
The radial oil seal is shaped by means of a vulcanisation process. The reinforcing ring is bonded to the elastomer component and the plastic and rubber mixture develops into its rubber-elastic state. The radial oil seal now achieves its final mechanical properties.
The sealing edge has already been created in the moulding tool or is parted off at this point. The spring is then fitted.
What properties do the standard materials display?
Radial oil seals are available in two standard elastomer materials and two PTFE materials. We can supply both either immediately from our stores or at short notice.
NBR Acryl Nitrile Butadiene Rubber
- The material most frequently used for radial oil seals. Good mechanical properties, a high degree of resistance to mineral-oil-based lubricating oils and lubricating greases. Good resistance to fuels can normally only be achieved from special mixtures.
- Properties are primarily determined by the proportion of ACN. A low proportion results in a high degree of flexibility at low temperatures, however restricted resistance to oils and fuels. As the proportion of ACN is increased, flexibility in cold conditions is reduced while resistance to oil and fuels rises.
- The standard NBR material for radial oil seals displays an average proportion of ACN, with these balanced properties covering a wide range of applications. Mechanical-technological values are high: a high degree of resistance to abrasion and good resistance to mineral-oil-based lubricating oils and greases, hydraulic pressure oils H, H-L, H-LP, non-flammable pressurised fluids HFA, HFB, HFC, aliphatic hydrocarbons, silicone oils and silicone greases, water temperature up to approx. +80°C.
- NBR provides no resistance in aromatic and chlorinated hydrocarbons, polar solvents, fuels with a high aromatic content, glycol-based brake fluids and non-flammable HFD pressurised fluids.
- While the degree of resistance to ozone, weathering and ageing is low, in most cases this does not have a disadvantageous effect, for example when the material is treated with a coating of oil.
FPM – Fluorine Rubber
- Outstanding resistance to temperature and chemicals, outstanding resistance to ageing and ozone and low level of gas permeability, self-extinguishing reaction to fire.
- Optimum resistance properties in mineral oils and mineral greases, synthetic oils and synthetic greases. Similar properties in aliphatic, aromatic and chlorinated hydrocarbons, fuels and non-flammable pressurised fluids HFD, and many organic solvents and chemicals.
- Provides no resistance in hot water and steam, polar solvents, glycol-based brake fluids and low-molecular organic acids.
PTFE – Polytetrafluoroethylene
- Fluorinated plastic, physiologically non-harmful. Provides an almost universal range of resistance to chemicals, a wide thermal range of application
(-90°C to +250°C) and a very low abrasion coefficient. Very high resistance to ozone, weathering and ageing.
For radial oil seals, use is normally made of PTFE compounds with filler materials such as carbon, graphite or glass fibre. - PTFE is used for sealing lips, coatings on sealing lips and entire radial oil seals, as soon as specific demands are made in terms of media resistance, thermal resistance, low abrasion or greater pressure and rotational speed.
What properties do the special materials display?
The special materials are used for special peripheral conditions.
HNBR – Hydrated Acryl Nitrile Butadiene Rubber
- Improved resistance to heat, ozone and ageing.
- Good mechanical properties, for example resistance to wear.
- Media resistance properties comparable with NBR.
NBR High Nitrile
- Higher resistance to oil and fuels than standard NBR.
NBR High Temperature
- Wider temperature application range than standard NBR, can be used at constant temperatures of up to +120°C.
NBR Low Temperature
- Wider minus temperature application range, can be used at temperatures between –50°C and +90°C.
NBR Graphite / NBR MoS2
- The addition of certain filler materials provides optimised-abrasion running properties.
MVQ – Silicone Rubber
- Wider range of thermal application, outstanding resistance to ozone, weathering and ageing.
- Restricted mechanical properties.
- Generally physiologically non-harmful.
- Can be used in temperature ranges from –50°C to +200°C.
- Resistant to aliphatic engine and transmission oils, animal and plant oils and fats.
- No resistance to fuels, aromatic mineral oils, steam, silicone oils and silicone greases, and to acids and alkalis.
ACM - Acrylate Rubber
- High resistance to engine, transmission and ATF oils.
- Range of application between NBR and FPM.
- Can be used at temperatures between –25°C and +150°C.
EPDM – Ethylene Propylene Diene Rubber
- Good resistance in hot water and steam, detergents, caustic potash solutions, silicone oils and silicone greases, many polar solvents and many diluted acids and chemicals.
- Wide range of thermal applications.
- Totally unsuitable for use with lubricants and fuels.
The sealing mechanism: how does this behave in terms of static tightness at the external surface?
The primary function of the radial oil seal is to guarantee static tightness in the casing bore.
The other requirements imposed on the external surface:
- To guide and guarantee the secure seating of the radial oil seal in the bore.
- To facilitate assembly by means of chamfers and curvatures.
- To provide compensation for gaps by means of a variety of heat expansion coefficients.
In the final analysis, the selection of the correct external surface depends on the specific application and the predominating operating conditions.
What is the dynamic sealing mechanism?
The functional principle by which the radial oil seal operates is that the elastomer sealing edge floats on the rotating surface of the shaft. The sealing edge is pressed against the surface of the shaft in a radial direction, as the internal diameter of the sealing lip in its tension-free state is smaller than that of the shaft diameter.
The radial force generated on the contact area is supported by means of a metallic screw tension spring to counteract the gradual decrease in the radial force.
The sealing effect at the elastomer sealing edge is achieved for the functional statuses of the shaft at a standstill and for the rotating shaft, and depends on the following parameters:
- the geometry of the sealing lip
- the properties of the elastomer material
- the design of the spring
- the surface finish of the shaft
- the lubrication status.
What provides the sealing effect with the shaft at a standstill?
In this case, it is provided by the radial contact pressure of the sealing lip exerted on the twist-free milled surface of the shaft. A radial force exerted on the shaft. The contact pressure against the sealing lip is achieved by means of pre-tensioning and is supported by the screw tension spring. The release of the elastomer pre-tensioning effect during operation is dependent on the operating parameters.
What provides the sealing effect with the shaft turning?
The rotational movement of the shaft produces a hydrodynamic effect. This results in the sealing lip floating over the film of lubricant formed by the medium to be sealed. This protects the sealing lip from premature wear and thermal destruction.
What is the reaction to permitted speeds and rotational speeds?
In order to prevent excessively high temperatures at the sealing lip — which might result in a hardening of the elastomer or the formation of oil carbon deposits — the rotational speed must be limited.
For shafts of greater diameter, higher rotational speeds are permitted than for shafts of lesser diameter. The reason for this is that the shaft cross-section increases in relation to the square of the diameter, and this gives rise to considerably more favourable possibilities for heat dispersal.
What role is played by the temperature?
As a result of the rotation of the shaft and the friction this creates at the sealing lip, the actual temperature at the sealing lip is higher than in the oil sump. This temperature differential represents the excess temperature. It is dependent on the following factors:
- rotational speed
- lubrication status / oil level
- heat dispersal
- pressure load
- surface finish of the shaft
- the material of the radial oil seal.
As the rotational speeds increase, the excess temperature at the sealing lip rises correspondingly. If the maximum permitted operating temperatures for the various elastomer materials are exceeded, this gives rise to premature hardening and increased wear.
What is the reaction to the media to be sealed?
The chemical resistance of the radial oil seal to the media in use has a crucial effect on the service life of the seal.
- To seal aggressive media, for many application cases construction types A/AS in the material FPM are more suitable than construction types in NBR.
- Radial oil seals in FPM withstand higher chemical and thermal loads.
- Construction types A/AS equipped as standard with stainless and acid-resistant steel springs, with the metallic reinforcing ring provided with an elastomer coating.
- For even greater requirements in terms of media resistance, we recommend the construction types WCP21 and WEPO.
- For mineral oil-based oils and fats, a good level of resistance is provided by the standard materials NBR and FPM. For synthetic oils and fats, resistance problems might possibly arise due to a variety of factors.
Friction statuses and lubrication.
In the interaction of the machine components of the shaft, radial oil seal and lubricant, we have three components or materials coming together. This gives rise to a tribological system. At any point of friction, the lubricant is of equal status with the solid components. It influences the operating reliability and service life of the tribological system to a great extent.
- 1. Dry running
- Under no circumstances must the shaft be allowed to rotate against the radial oil seal without lubrication. Accordingly, on assembly the sealing lip
of the radial oil seal must be lightly greased.
Dry-running applications call for special construction types and materials, such as radial oil seals with a PTFE sealing lip. - 2. Greasing
- Where lubrication is purely by greasing, the dispersal of friction heat is considerably less than in the case of oil lubrication. This type of greasing
should only be used with slowly rotating shafts.
For sealing slowly rotating shafts, the space between the radial oil seal and the bearing should be almost completely filled with grease. If there is no suitable lubricating grease available, we recommend using a radial oil seal with a PTFE sealing lip. - 3. Sealing media with poor lubricating properties
- In this case, to achieve adequate lubrication of the sealing edge, a grease filling between the sealing and the protective lip (maximum two thirds of the space) must be provided. Even more effective is a pair of radial oil seals arranged one after the other with an intermediate grease filling (maximum two thirds) to make secondary lubrication possible.
- 4. Hydrodynamic sealing aids
- Where the normal feed effect of the radial oil seal is inadequate, so-called "rifling" can be used as an additional hydrodynamic sealing aid. This takes the form of raised return feed ridges. The way in which the rifling works corresponds to that for a simple threaded shaft seal.
Pressure as an operating parameter.
- 1. Non-pressurised operation
- Radial oil seals are generally designed for non-pressurised operation.
- 2. Operation under pressure
- The load combination of pressure and rotational speeds is crucial for the selection of the correct radial oil seal ring.
- 3. Pressure load for standard construction types
- Standard radial oil seals are designed to still be adequate for very low pressures and seal spaces with slight pressure differentials, for containing fluids, greases and air.
What is achieved by construction type V as a pressure-bearing version?
We recommend construction type V for pressure differentials greater than 0.5 bar, pulsed pressures and vacuum applications.
This construction type is designed with a short reinforced sealing lip with a metal cage below it. As a result of the pressure, the increase in contact force is reduced, with the greater abrasive effect and premature wear being reduced.
What is the function of supporting rings?
Pressure differentials greater than 0.5 or can also be sealed using a standard radial oil seal and an additional steel supporting ring. This combination caters for pressures — depending on speed — of up to around 10 bar. Only construction types without a protective lip can be used.
Everything you need to know about the installation space.
- 1. The shaft
- The shaft is a crucial element in the rotation-sealing system. It must fulfil a number of technical requirements if it is to guarantee
an effective sealing effect.
The exact design of the shaft in the running surface area of the radial oil seal's sealing edge is also crucial for the service life and sealing function of the rotation-sealing system. - 2. Tolerances (DIN 3760)
- ISO Tolerance Range h11 should be applied for the shaft diameter d1 in the running surface area of the radial oil seal's sealing edge. Tolerance Class IT 8 (DIN ISO 286) is required for the roundness of the shaft.
- 3. Surface finish of the shaft
- The shaft must be processed so that it is round at its running surface area. If the surface of the shaft is too rough this will result in premature wear in the sealing edge.
- 4. Surface hardness of the shaft
- Another factor crucial for the service life of the sealing point is the hardness of the running surface on the shaft. In terms of surface hardness, an effective hardening depth of at least 0.3 mm is required. The decision on the suitability of individual shaft surfaces (chrome-plated, cadmium-plated, nitration-hardened, phosphatised) must be taken on the merits of each individual case.
- 5. The running surface area
- The running surface area must be specified with reference to the width of the stipulated seal.
- 6. Processing the shaft surface
- In the running surface area of the sealing edge, the shaft must be milled twist-free and completely circular if the sealing function is to be guaranteed.
The following processing techniques can be used:- plunge-cut grinding
- hard turning
- 7. Twist-free shaft surface
- It is essential that the shaft's running surface area has been produced completely twist-free. Twist-free means that the traces left by processing do not run off at any angle.
- 8. Shaft materials
- The standard tempering steels are suitable as shaft materials, as long as the values for surface hardness are observed. Hard-chrome plated shafts
and plastic shafts are of limited suitability. The following statement applies generally for all shaft surface materials: the stipulated values in terms
of quality and hardness must be observed.
If the shaft is not provided with the required running surface properties, then use must be made of corresponding shaft protection sleeves. Dichtungspartner Hamburg offers you a range of shaft protection sleeves in all dimensions and in a variety of materials. - 9. Radial run-out
- Any radial run-out or dynamic eccentricity in the shaft must be kept to an absolute minimum. Accordingly, the radial oil seals should be fitted in the immediate vicinity of the bearing and bearing play minimised.
- 10. Shaft chamfer
- The sealing lip must not be damaged on installation, to ensure that the sealing lip is not angled over.
- 11. Damage to the shaft
- It is essential that no damage of any kind is caused to the running surface of the shaft. We recommend that shafts be carefully protected in transit between production and assembly. Transportation devices or specially cast or slide-over protective plastic sleeves are suitable for the purpose.
About the casing bore.
The design and construction of the casing bore are crucial for static sealing. The following conditions must be fulfilled if a secure and tight seating in the casing bore is to be achieved:
- tolerances
- casing dimensions
- chamfer on the casing bore
- surface quality of the casing bore
The coaxiality of the casing bore results in uneven distribution of the contact force at the circumference. Numerous disadvantageous processes arise out of this situation. Accordingly, any discrepancy in coaxiality must be kept to a minimum.
In the selection of construction type for the radial oil seal and the material of the casing, consideration must be given to the heat expansion coefficient in all cases.
About heat expansion.
The heat expansion properties of the material of the radial oil seal and of the casing are important for the static sealing process in the casing bore. From the thermal point of view, casings made of steel or cast iron offer the greatest advantages, used in combination with a radial oil seal with a rubberised external cover.
About an offset angled position.
The installed radial oil seal must be centred as far as possible and installed perpendicular to the shaft.
About the degree of rigidity.
Casings are frequently designed with thin walls. When fitting radial oil seals into thin-walled casing bores or seating recesses of lesser rigidity, the problem of the casing being severely expanded can arise. We recommend the use of radial oil seals with a rubberised external cover or using another casing bore tolerance.
Split casings.
Thanks to the good elastic malleability of elastomer and of the mould filler, the required degree of static sealing can be achieved with construction type A. This means that even split casings featuring a variety of split levels and even an offset separation joint can be reliably sealed.
All about installation.
Proper installation is crucial. Radial oil seals are installed in accordance with DIN 3760.
Prior to installation, both the installation space and the radial oil seal should be carefully cleaned. Ideally, a hydraulic or mechanical pressing device should be used to push the radial oil seal into the casing bore. The pressing tool should be held in its final position for some time. Where the radial oil seal has to be guided over sharp-edged shoulders, the appropriate installation sleeves should be provided. The sleeve itself must not display any damage or rough surfaces. For the radial oil seal to be securely seated, the external cover must be located completely within the casing bore.
All about special applications.
- 1. Under-pressure or vacuum sealing
- To seal a shaft against under-pressure use is made of radial oil seals corresponding to the pressure gradient at the sealing lip on the atmospheric side. Where grease is used, the outer radial oil seal must also be installed with its sealing lip facing out to the atmospheric side.
- 2. Separating two media
- To separate two spaces containing different media one from the other, use is made of two radial oil seals with their sealing lips facing in opposite directions. A further option for separating two media at lower to medium rotational speeds is the use of our construction types AD and BD, which in their design combine two sealing lips arranged in opposite directions within a single seal.
- 3. Sealing in the presence of severe external dirt/contamination
- The effects of external dirt and contamination result in premature wear to both seal and shaft surface. Depending on the type and quantity of the contamination arising, protection should be provided for the sealing lip. Under extreme conditions — such as with agricultural and construction machinery — cassette seals should be used.
- 4. Sealing with contaminated media
- Contaminated media or media containing abrasive materials cause a high degree of wear in the area of the seal. This can be countered by installing a second seal before the first, or with the use of our VRM axial seal.
Correct storage of elastomer products.
In their specific properties, elastomers remain practically unchanged for a period of years, as long as certain minimum requirements in terms of their storage conditions are observed (refer to DIN 7716 and ISO 2230).
- Seals should be stored free of tension.
- They should be protected from any pronounced change of air. We recommend storage in a polyethylene bag or in airtight containers.
- Storage conditions cool, dry, low-dust and only moderately ventilated.
- Storage temperature not below –10°C and not above +20°C.
- Heat sources/radiators should be screened and kept at a distance of at least one metre.
- Relative humidity should not exceed 65%.
- Strong lighting (above all UV radiation and direct sunlight) should be avoided.
- No use should be made of electrical equipment generating ozone.
Types
![]() 827 N Form A |
![]() 827 S |
|
![]() 827 NW |
![]() 827 SW |
|
![]() 827 NRDW |
![]() 827 SLDW |
|
![]() 827 SS |
![]() 827 D |
|
![]() 827 NK |
![]() 827 SK |
|
![]() 827 NV |
![]() 827 SV |
|
![]() 827 NO |
![]() 827 SO |
|
![]() 829 NRDW |
![]() 829 SLDW |
|
![]() 822 N Form B |
![]() 822 S |
|
![]() 822 NRD |
![]() 822 SRD |
|
![]() 822 SS |
||
![]() 822 NK |
![]() 822 SK |
|
![]() 824 N Form C |
![]() 824 S |
|
![]() 822 D |
![]() 824 D |
|
![]() 820 N |
![]() 820 S |
|
![]() 820 D |
||
![]() 875 N |
||
![]() 870 N |
||
![]() 835 N |
![]() 835 S |
|
![]() 835 D |
![]() 830 D |
|
![]() 830 N |
![]() 830 S |
|
![]() 826 N |
![]() 826 S |
|
![]() 823 N |
![]() 823 S |
|
![]() 821 SSP |
![]() 821 SS |
|
![]() 825 N |
![]() 825 S |
|
![]() 825 N |
![]() 825 S |
|
![]() LR 891 W |
![]() LR 890 W |